SCOTT M. BOYLE
TECHNICAL DIRECTOR
3D Printing
Professional Development and Research
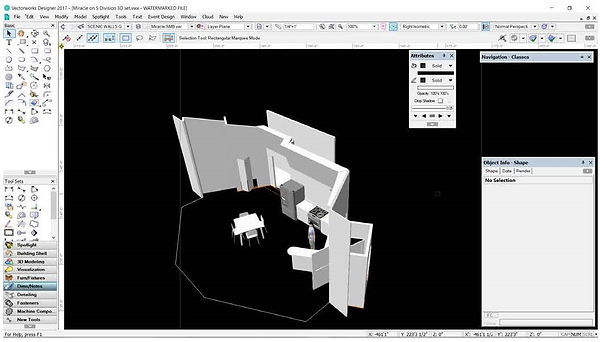
3D Printing in Theatre
From attending various USITT national conferences and speaking with colleagues around UMD, I became increasingly interested in 3D printing. At first I was considering it mostly for building props for shows, but I soon learned I could do a lot more. I requested a MakerBot through "Technology Fees" in the Fall of 2016 to see how the Department of Theatre may start to utilize this technology.
I didn't pursue it very much until I took Curtis Phillips' CAD class and learned how to use Vectorworks better. During the final project I created a 3D model of a set I had worked on for Peninsula Players. As I was looking for something else in a menu bar, I came across an export function which had a file extension commonly used in 3D printing. I decided to see what I could do with it.
This is a screen shot of the model after I had drafted it in Vectorworks.
You're going to need a bigger printer.
You can't 3D print directly from Vectorworks. The model has to go through another program to ensure everything is intact and an internal structure constructed before it can be printed. As my needs are rather basic, the base software that came with the MakerBot was good enough for this function. There are other programs such as MeshMixer which can do far greater manipulations with 3D models.
After the I imported the file, the model was too big to print. As shown in the screen shot to the right, the model surrounds the footprint of the printer shown as the red box. I had to convert the height of the tallest wall from the scale it was drawn to millimeters so it would fit.


Ready to Print
Once I had the model so not only it was a size the MakerBot could handle but also a scale commonly used it theatrical models (1/4" = 1'-0" in this case) I could begin the printing process. This model took roughly 10 hours to print. Once the file was sent to the printer, the computer the file came from could go to sleep without it harming the printing process. I calculated the cost of the printing was less than a dollar, far less than the supplies usually associated with building theatrical models.

Final 3D printed model
Antigone pillars
I was surprised to see how fast this knowledge would come in handy. Our first production of the 2017 season featured these very interesting columns which were based off of actual columns in a government building. One corner was square but as you can see in this screen shot, the columns had curves on two different planes. This was going to make them difficult for most of the students working in the shop to visualize what they looked like or how we'd build them.

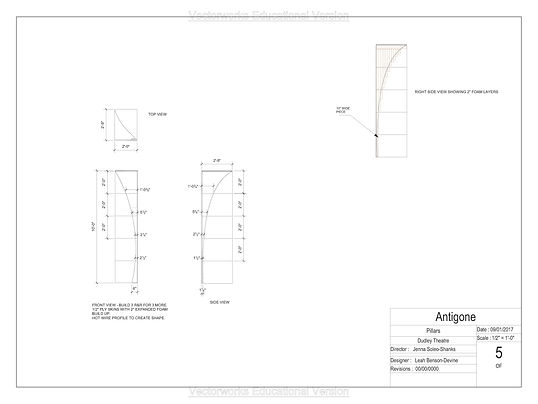
Conventional drawings didn't make it very clear what the object looked like.
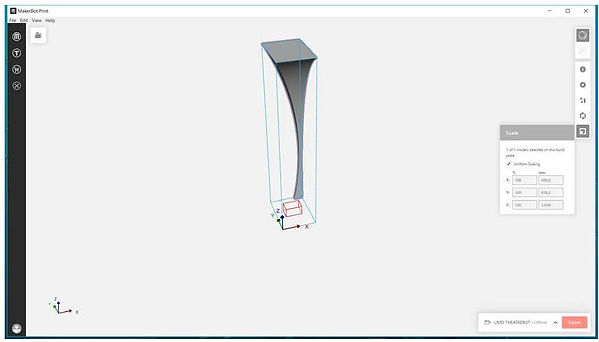